My wife and I were traveling in the Phoenix, AZ area, and as is our usual custom, we looked for fellow clock and watch nerds to chat up. Some googling […]
Categories
Road trip – Scottsdale AZ
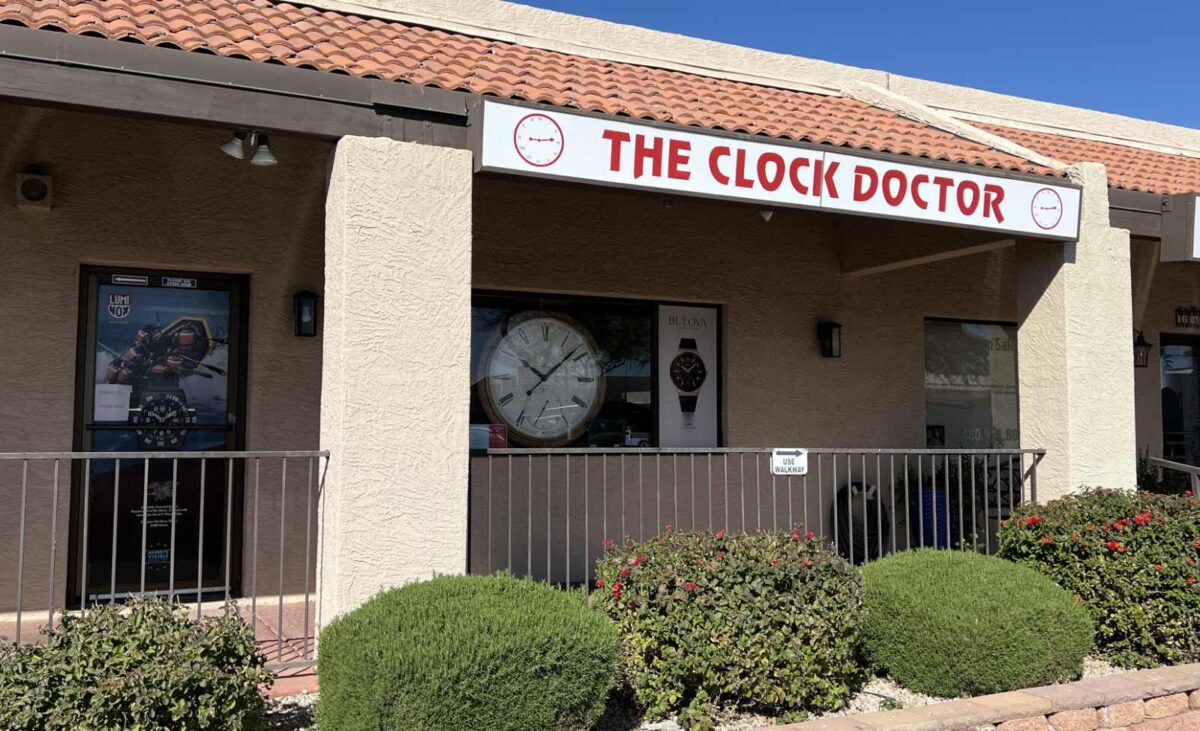
My wife and I were traveling in the Phoenix, AZ area, and as is our usual custom, we looked for fellow clock and watch nerds to chat up. Some googling […]
As of January 2023, the Minnesota Clockmaker’s Guild and MWCA have combined to form the Minnesota Horological Society. We meet monthly, usually at the Hopkins Pavilion to discuss a watch […]
A quick trip to Milwaukee surprises with fantastic clocks
The Minnesota chapter of the NAWCC called the OT Lang Memorial chapter meets the third Saturday of every odd month. The topic for May was “My favorite clock or watch”. […]
A preview of the soon to open Cuckoo Clock Museum near Downtown Minneapolis